AI-driven flow rate control for reliable 3D printing
3D printing has emerged as a groundbreaking technology, enabling the creation of intricate, customized products on demand. However, this method is not without its challenges. Errors such as over-extrusion, under-extrusion, and misalignment of layers can compromise the quality of printed objects, often requiring human intervention or extensive post-processing. To tackle these challenges, we have developed a system that leverages artificial intelligence (AI) to detect and correct these errors in real-time, making 3D printing more reliable and efficient.
The challenge of consistency
In the realm of 3D printing, objects are constructed by sequentially depositing material layer by layer through a nozzle. While this method offers unparalleled flexibility and customization, it is also susceptible to inconsistencies. Variations in the material flow rate, changes in nozzle speed, and environmental factors can all lead to defects that degrade the final product.
Historically, correcting these issues has involved manual adjustments, with operators relying on experience and trial-and-error methods. However, as 3D printing scales to more complex and high-volume production, this manual approach is becoming increasingly impractical. Real-time, automated solutions are necessary to ensure consistent quality across multiple machines.
Data collection and AI model training
To address these challenges, our research introduces an AI-powered system designed to monitor and adjust the 3D printing process as it unfolds. The system is equipped with a camera that captures detailed images of the material as it is extruded from the printer nozzle. In addition to this visual data, we also collect critical operational data from the printer itself, such as the speed, the temperature, and the rate at which material is being extruded.
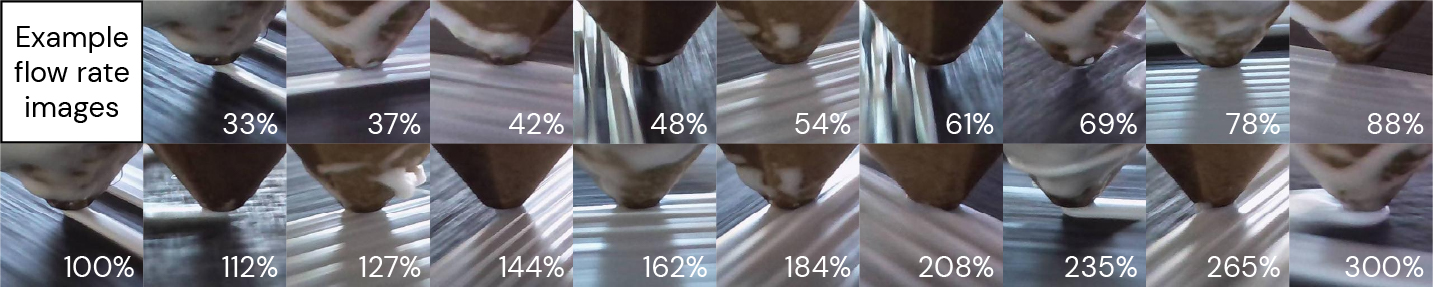
The core of our system is a deep learning regression model based on RegNet architecture, which is well-suited for image recognition tasks. We trained this model on a dataset of over 250,000 images, each labelled with the corresponding extrusion rate active at the time the image was captured. To enhance the model’s ability to generalize to different printing conditions, we applied various data augmentation techniques. These included adjusting image colours, flipping images horizontally, and randomly cropping them to simulate a wider variety of scenarios.
Real-time error detection and adjustment
Once trained, the AI model can estimate the distance from optimal material flow rate as a percentage based on the real-time images captured during the printing process. If the model detects any deviation from the desired flow rate—whether due to over-extrusion, under-extrusion, or poor calibration—it can immediately adjust the printer settings to correct the issue. This real-time feedback loop helps to prevent errors from accumulating, ensuring a higher quality print from start to finish.
Our tests showed that the model could make predictions at a rate of 100 times per second on a single computer chip, outpacing the printer’s own speed. This high prediction rate means that the AI can be used to monitor multiple printers simultaneously or be integrated with other systems to further enhance print quality.
Adapting to new materials
One of the significant challenges in 3D printing is adapting to new or unfamiliar materials. To test the adaptability of our AI system, we used a material known as foaming PLA, which changes shape and size depending on the temperature. This presented a unique challenge, as the optimal flow rate for this material could not be predetermined.
We allowed our AI system to learn the optimal flow rate for foaming PLA in real time as the material was printed at varying temperatures. The system successfully predicted the correct flow rate adjustments for each temperature change, ensuring smooth and accurate prints without prior calibration. This capability to self-learn and adapt to new materials underscores the versatility of our AI approach.
On the fly error correction
We also tested our system on a part resembling a spanner, where we deliberately introduced errors by reducing the flow rate to half its optimal value. In the first test, where the flow rate remained unchanged, the print quality was significantly compromised. However, when we allowed our AI system to intervene, it quickly detected the error and corrected it, resulting in a much-improved final product.
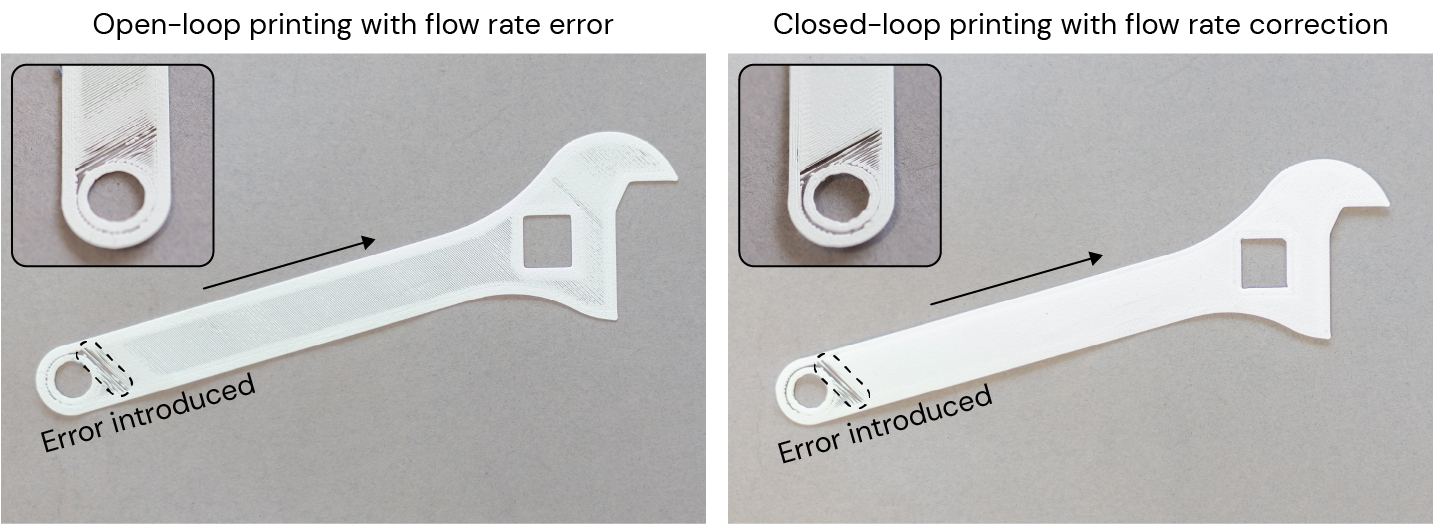
Our system’s ability to make rapid adjustments—without requiring multiple attempts—demonstrates its effectiveness. We further fine-tuned the system to minimize unnecessary adjustments by controlling the response speed based on the proximity of the prediction to the optimal value. This refinement ensures that the system only makes critical corrections, reducing the risk of over-adjustment and further improving print quality.
AI-driven control for wider manufacturing
Looking to the future, we believe that the principles behind our AI-driven approach can be extended to other manufacturing processes, offering new possibilities for intelligent, automated production systems. As we continue to refine this technology, we aim to push the boundaries of what’s possible in the world of manufacturing.
Further Reading
Read the paper
Authors
Douglas A. J. Brion
Sebastian W. Pattinson