Spearheading a new approach to automated quality control
Unlike existing inspection systems, Blue-1 adapts to different environments, products, and processes, delivering highly accurate results with minimal setup time and capital outlay.
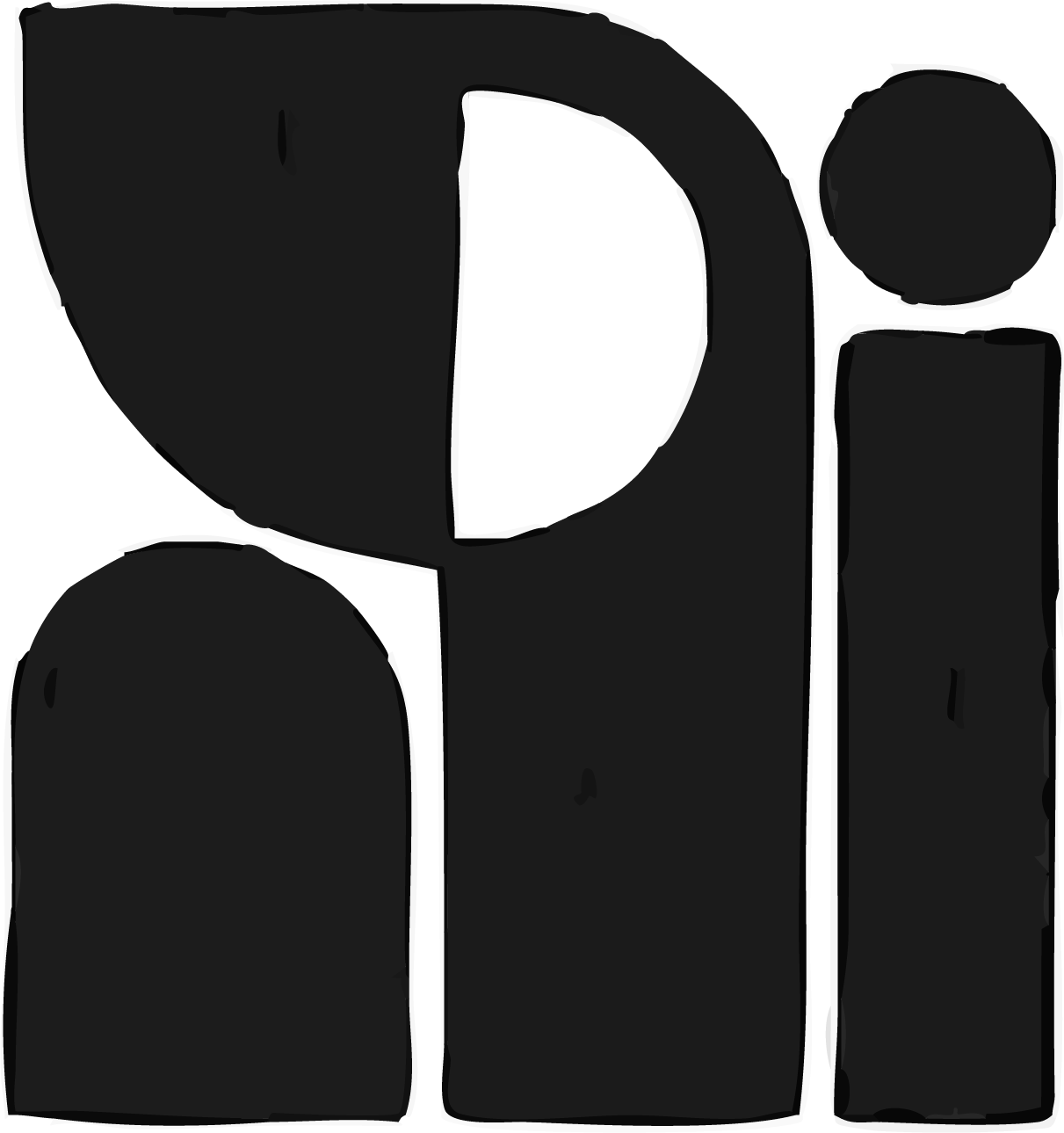
Robust
Works across lighting conditions, environment, and positions.
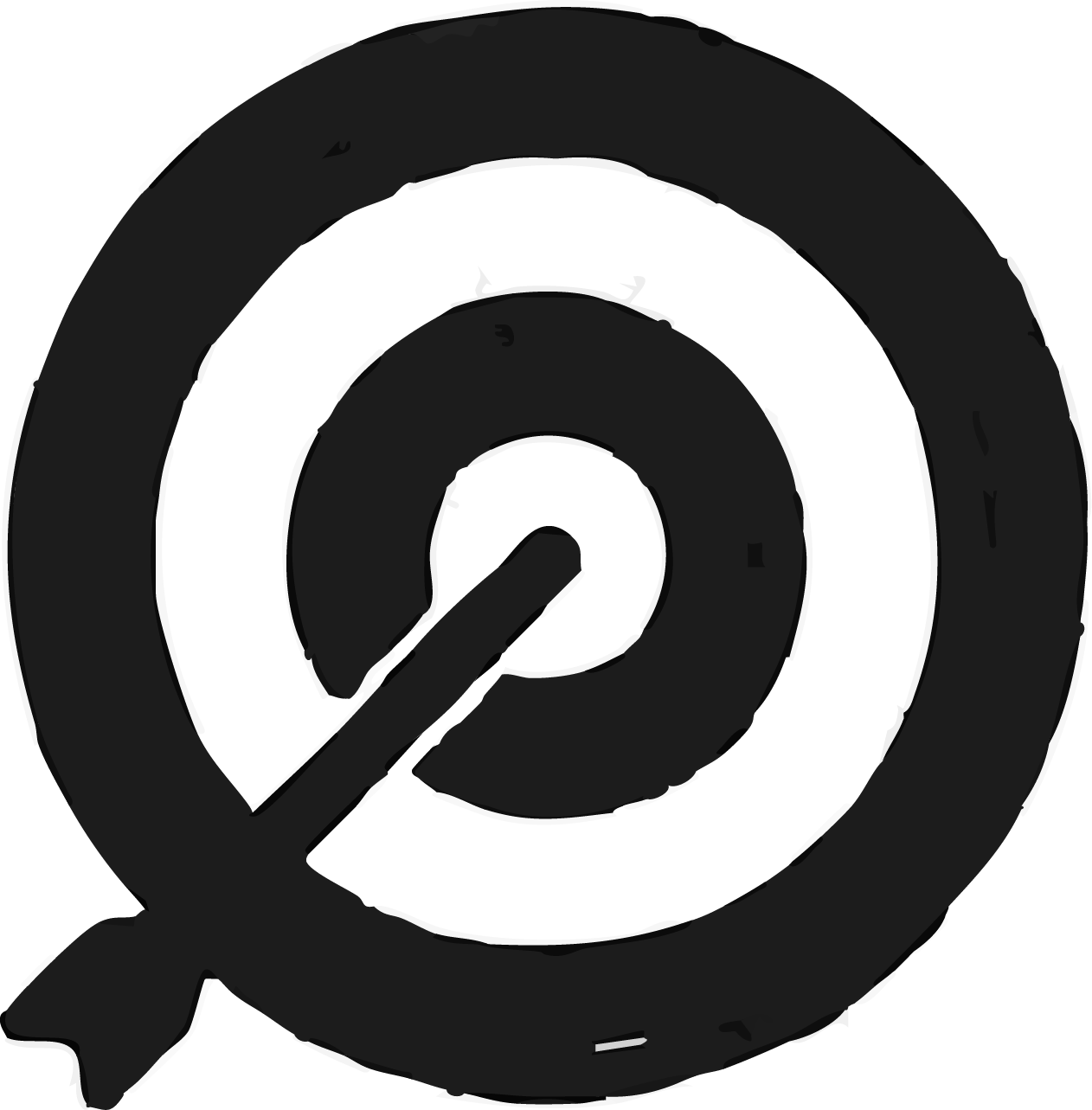
Accurate
Surpasses 99.9% in accuracy in most tested manufacturing contexts.
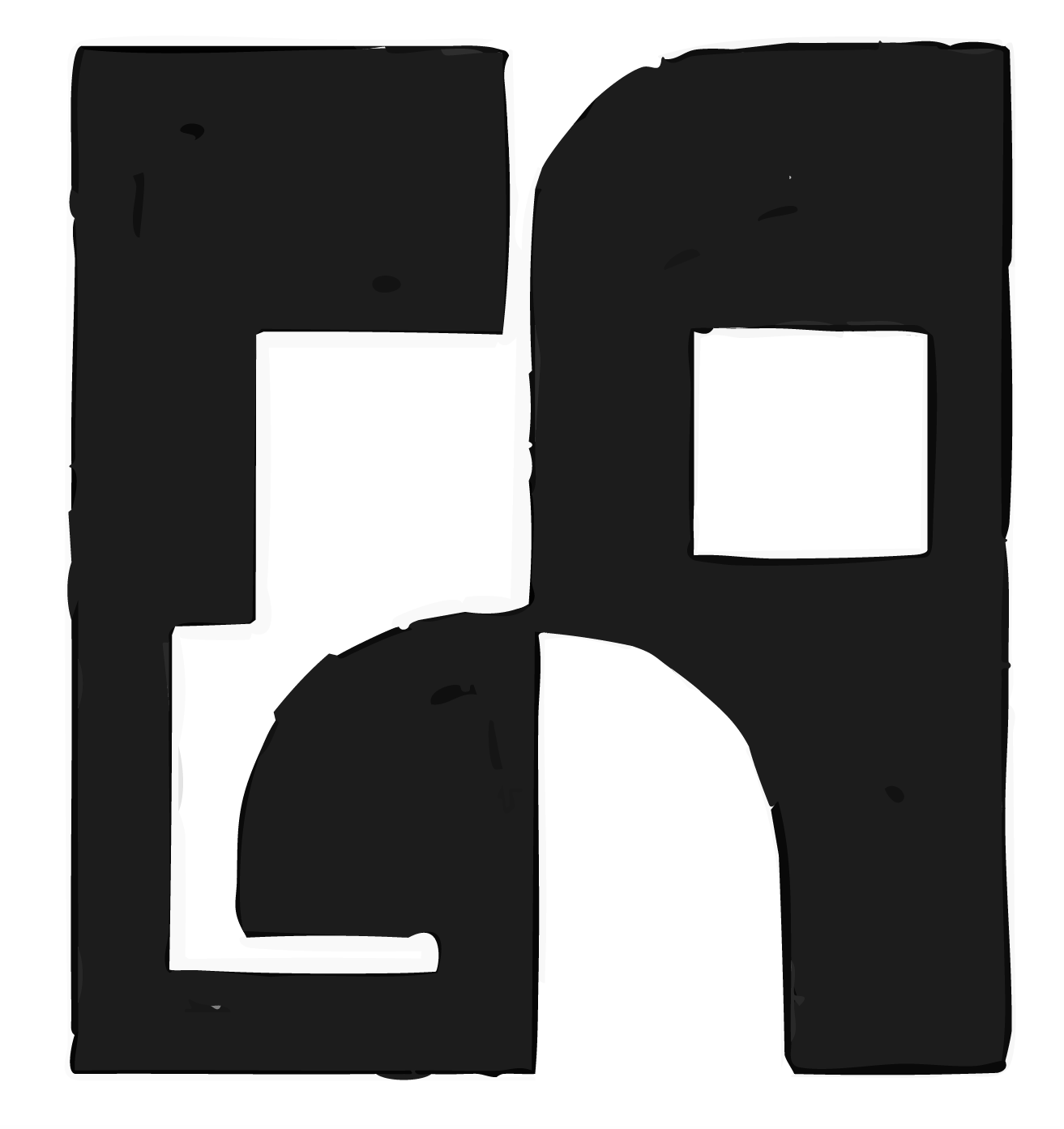
Rapid setup
Adapts to a new process or product with only a couple of hours of data.
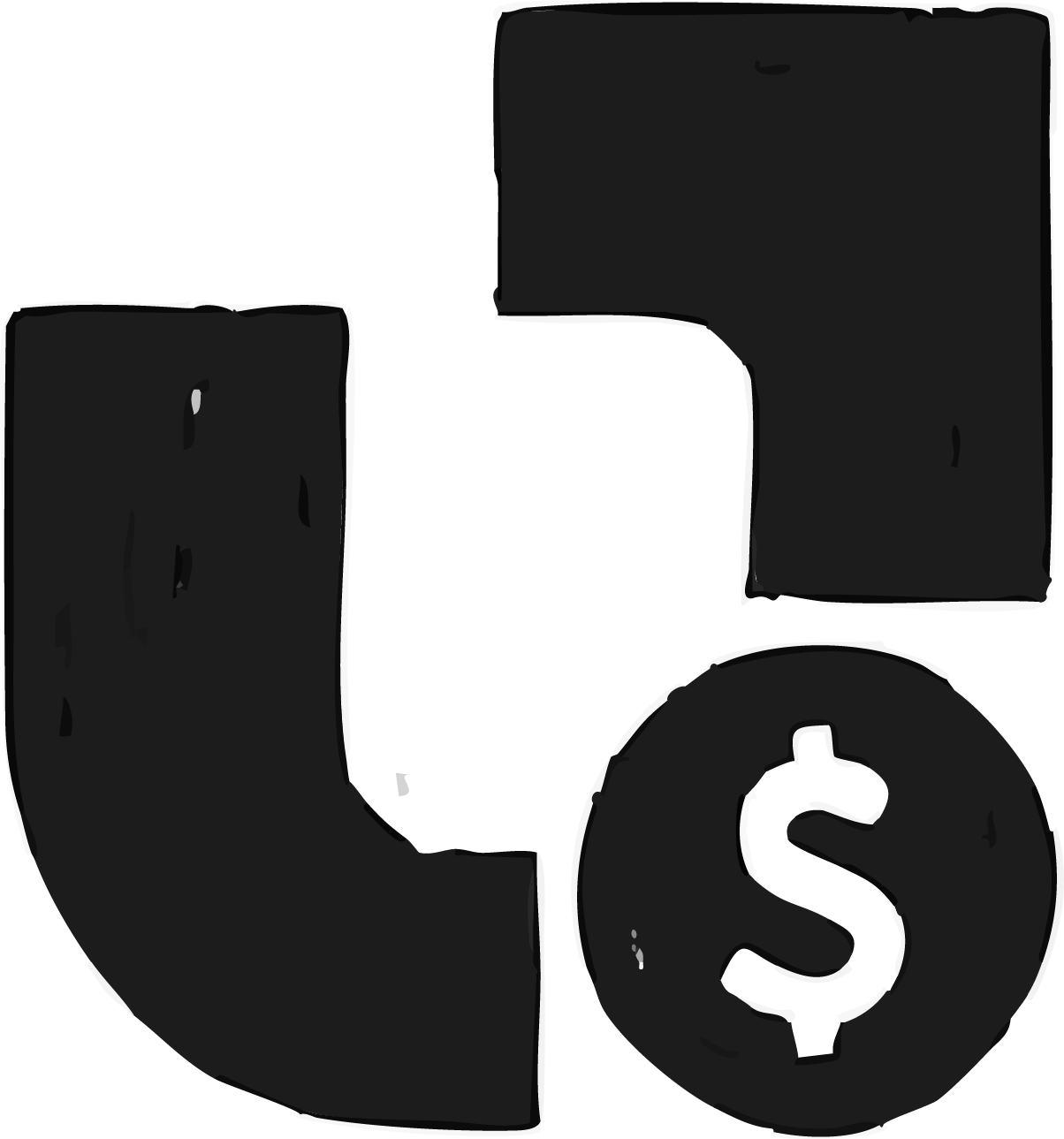
Low-cost
Simple, off-the-sheld industrial hardware, that we install at cost.
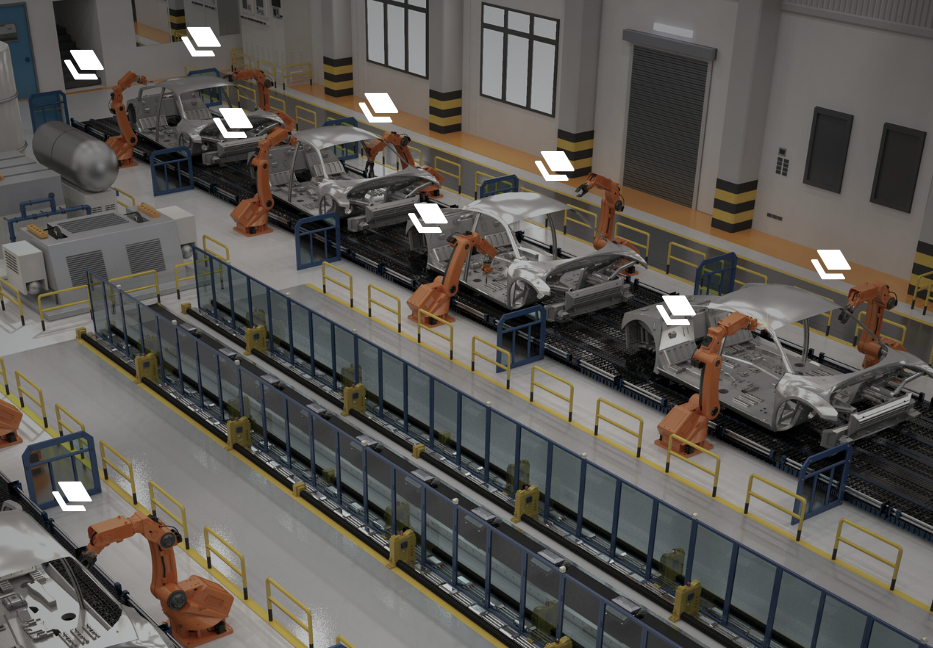
Full production visibility
Low upfront cost and fast installation time means you can deploy our kit at every step in your manufacturing line, gaining complete transparency on your operations.
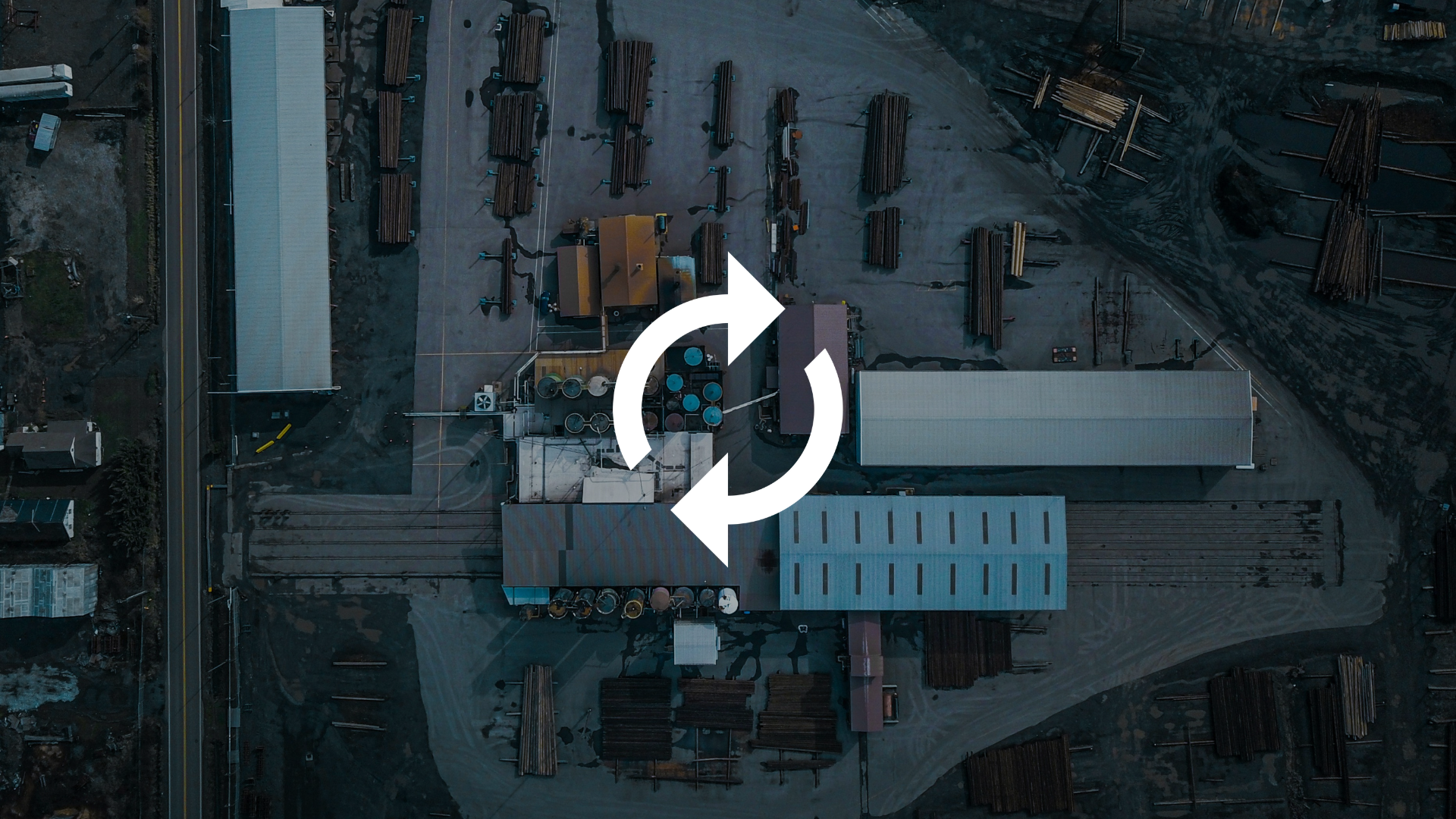
Reconfigure based on demand
Rapid adaption to a completely new products or processes, means that changes to your product, lines, or demand can be met.
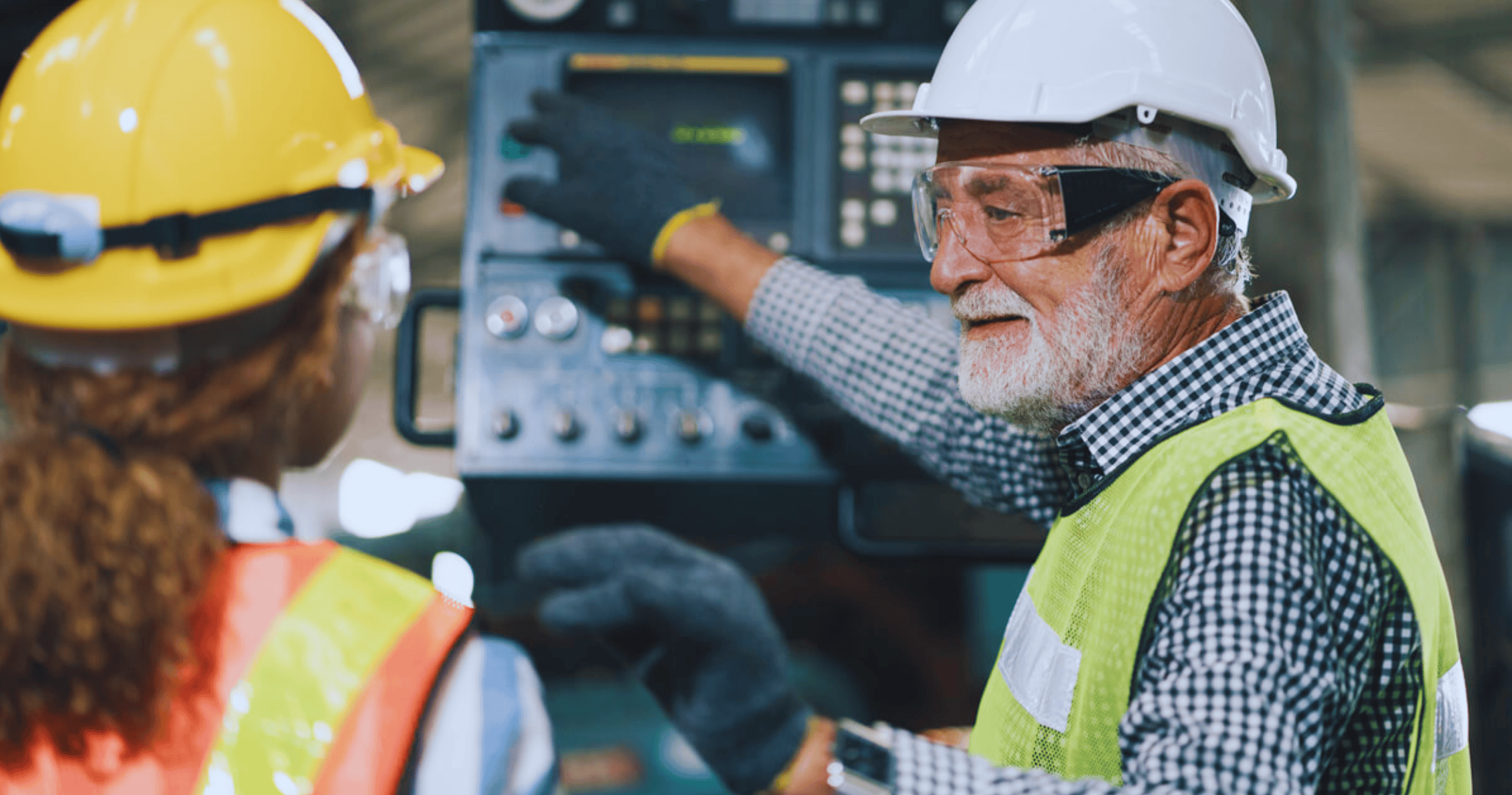
Capture tribal knowledge
With supervision, Blue can capture some of the knowledge of your expert operators, democratise this knowledge to trainees and help upskill your workforce.